An Unbiased View of Alcast Company
The Greatest Guide To Alcast Company
Table of ContentsThe Greatest Guide To Alcast CompanyOur Alcast Company IdeasEverything about Alcast CompanyGet This Report about Alcast CompanyAn Unbiased View of Alcast CompanySome Known Details About Alcast Company
The subtle difference depends on the chemical content. Chemical Comparison of Cast Light weight aluminum Alloys Silicon promotes castability by lowering the alloy's melting temperature and boosting fluidness during casting. It plays a critical function in allowing detailed mold and mildews to be loaded properly. Additionally, silicon adds to the alloy's toughness and put on resistance, making it important in applications where longevity is important, such as automotive parts and engine parts.It additionally boosts the machinability of the alloy, making it less complicated to refine right into finished products. In this means, iron adds to the total workability of aluminum alloys.
Manganese adds to the strength of light weight aluminum alloys and boosts workability (aluminum casting company). It is generally used in functioned aluminum products like sheets, extrusions, and profiles. The existence of manganese aids in the alloy's formability and resistance to fracturing throughout fabrication processes. Magnesium is a light-weight component that provides strength and influence resistance to aluminum alloys.
The Best Strategy To Use For Alcast Company
Zinc enhances the castability of light weight aluminum alloys and assists control the solidification procedure throughout spreading. It improves the alloy's strength and solidity.
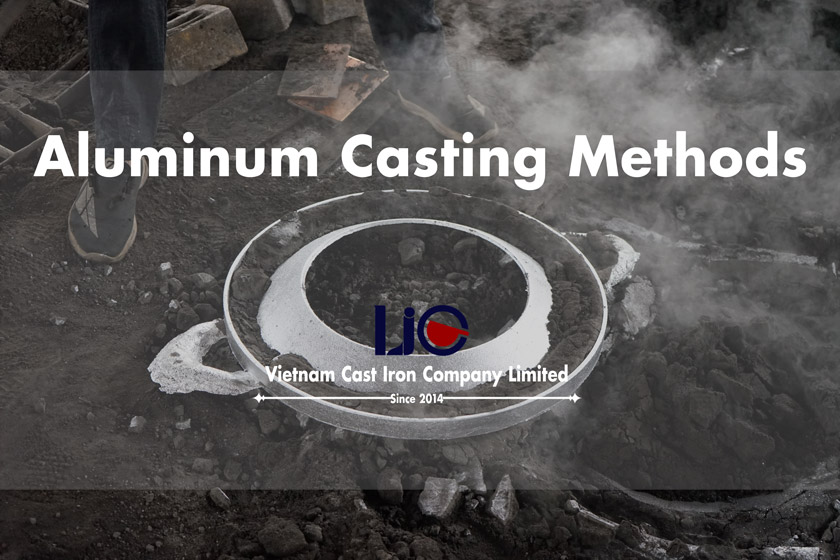
The primary thermal conductivity, tensile strength, yield stamina, and elongation differ. Among the above alloys, A356 has the highest thermal conductivity, and A380 and ADC12 have the lowest.
The Ultimate Guide To Alcast Company
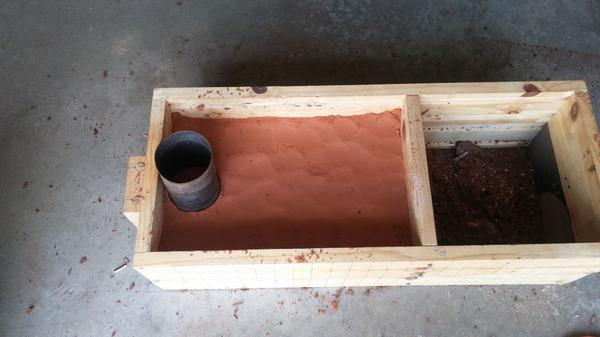
In accuracy casting, 6063 is well-suited for applications where detailed geometries and high-quality surface coatings are extremely important. Examples consist of telecommunication enclosures, where the alloy's remarkable formability enables sleek and visually pleasing styles while keeping architectural stability. In the Lighting Solutions market, precision-cast 6063 elements develop elegant and efficient illumination components that call for intricate shapes and great thermal efficiency.
The A360 shows premium elongation, making it ideal for complex and thin-walled components. In accuracy spreading applications, A360 is appropriate for markets such as Consumer Electronics, Telecommunication, and Power Devices.
The 7-Minute Rule for Alcast Company
Its distinct properties make A360 a valuable selection for accuracy casting in these sectors, improving item longevity and top quality. Aluminum alloy 380, or A380, is a widely made use of spreading alloy with numerous distinctive qualities. It provides outstanding castability, making it a suitable selection for precision spreading. A380 displays great fluidity when molten, ensuring complex and detailed molds are properly duplicated.
In precision spreading, light weight aluminum 413 radiates in the Consumer Electronic Devices and Power Devices markets. This alloy's exceptional corrosion resistance makes it a superb option for outside applications, ensuring durable, long lasting products in the mentioned sectors.
Unknown Facts About Alcast Company
When you have determined that the aluminum pass away casting procedure is ideal for your project, a critical next action is selecting one of the most suitable alloy. The light weight aluminum alloy you these details choose will considerably impact both the spreading process and the properties of the end product. As a result of this, you have to make your decision very carefully and take an informed technique.
Determining the most ideal light weight aluminum alloy for your application will certainly indicate evaluating a broad range of qualities. The first category addresses alloy characteristics that affect the production procedure.
The Buzz on Alcast Company
The alloy you choose for die spreading directly impacts several elements of the spreading procedure, like exactly how simple the alloy is to deal with and if it is susceptible to casting flaws. Hot cracking, likewise known as solidification breaking, is a normal die casting issue for aluminum alloys that can cause internal or surface-level splits or cracks.
Specific aluminum alloys are extra prone to hot breaking than others, and your option ought to consider this. It can harm both the cast and the die, so you need to look for alloys with high anti-soldering homes.
Deterioration resistance, which is currently a significant feature of aluminum, can differ substantially from alloy to alloy and is an important particular to take into consideration depending on the ecological problems your item will be subjected to (Aluminum Casting). Put on resistance is another home generally sought in aluminum items and can separate some alloys